- 賽事資訊
- 職教新聞
- 新聞專題
- 汽修專業(yè)
- 數(shù)控專業(yè)
- 電子專業(yè)
- 加工制造
- 機(jī)電專業(yè)
- 模具專業(yè)
- 電氣信息
- 旅游管理
- 建筑專業(yè)
- 信息技術(shù)
- 化工專業(yè)
- 機(jī)械制造
- 財(cái)經(jīng)專業(yè)
- 餐飲專業(yè)
- 酒店專業(yè)
- 商貿(mào)專業(yè)
- 醫(yī)藥衛(wèi)生
- 地質(zhì)勘察
- 交通土建
- 財(cái)經(jīng)商貿(mào)
- 鐵道工程
- 服裝設(shè)計(jì)
- 基礎(chǔ)課程
- 美容美發(fā)
- 農(nóng)林牧漁
- 包裝印刷
- 材料能源
- 法學(xué)專業(yè)
- 公共事業(yè)
- 生物工程
- 市場(chǎng)營(yíng)銷
- 資源環(huán)境
- 機(jī)器人
- 無(wú)人機(jī)
- 通用性技能知識(shí)
- 綜合
當(dāng)前位置:首頁(yè) > 文章資訊 > 機(jī)械制造 > 鍛造與沖壓:汽車輕量化之路,原來(lái)還能在這個(gè)方面發(fā)力!汽車熱沖壓成形(Hot Stamping)的技術(shù)要點(diǎn)解析!
鍛造與沖壓:汽車輕量化之路,原來(lái)還能在這個(gè)方面發(fā)力!汽車熱沖壓成形(Hot Stamping)的技術(shù)要點(diǎn)解析!
汽車熱沖壓成形(Hot Stamping)的技術(shù)要點(diǎn)解析!
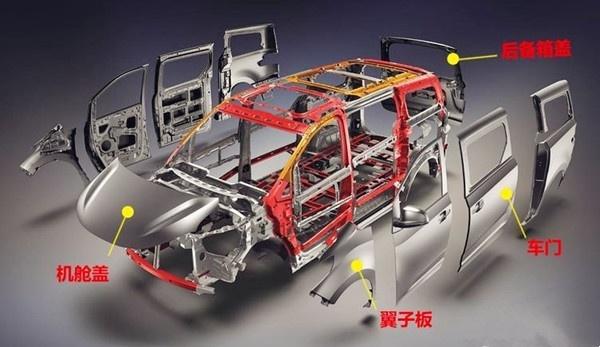
大排量、大馬力的快只是直路上的快,而輕量化的快則是無(wú)時(shí)無(wú)刻的快。隨著各國(guó)對(duì)于汽車排放、污染、環(huán)保等話題的深入,走大排量發(fā)動(dòng)機(jī)的路線顯然是難上加難。因此,輕量化成為眾多車企選擇的路徑。因此我們說(shuō)汽車輕量化是汽車重要的發(fā)展方向,也是世界各國(guó)實(shí)現(xiàn)節(jié)能、減排、降耗的重大舉措。
汽車行業(yè)雖可望扭轉(zhuǎn)產(chǎn)量下降的趨勢(shì),并獲得新的發(fā)展,但面對(duì)激烈的國(guó)際競(jìng)爭(zhēng),如何進(jìn)一步降低成本、制造適應(yīng)消費(fèi)者需求的汽車,形勢(shì)依然嚴(yán)峻。另外,還有諸如強(qiáng)化安全對(duì)策、以保護(hù)地球環(huán)境為目的并且針對(duì)溫室效應(yīng)的節(jié)省資源、能源的降低油耗、減少公害等方面的對(duì)汽車生產(chǎn)提出更高的要求。也許是改裝文化的深入,讓不少對(duì)汽車有一定興趣的群體,提及到輕量化第一時(shí)間想到的就是“快、性能、飆車”這些字眼。的確,輕1公斤真的是比增加10馬力還要快,但快其實(shí)只是結(jié)果之一,包括燃油經(jīng)濟(jì)性、排放等也是輕量化的正面效果。
超高強(qiáng)鋼熱沖壓構(gòu)件的應(yīng)用能夠在減輕汽車整車重量的同時(shí),保證車身強(qiáng)度及安全性,是實(shí)現(xiàn)汽車輕量化的重要途徑。汽車輕量化之路,原來(lái)還能在這個(gè)方面發(fā)力!
本文主要介紹作者所在的研究團(tuán)隊(duì)圍繞超高強(qiáng)鋼汽車構(gòu)件熱沖壓成形技術(shù)及裝備所做的部分研究工作。
汽車輕量化是汽車重要的發(fā)展方向,也是國(guó)家重大科技需求。燃油車整車重量每降低10%,燃油效率提升6%~8%,排放下降4%;純電動(dòng)車、混合動(dòng)力車等新能源汽車對(duì)重量更加敏感,整車每減重10%,續(xù)航里程增加10%~15%。
高強(qiáng)度輕量化材料在汽車上的應(yīng)用能有效地推進(jìn)輕量化進(jìn)程?!吨袊?guó)制造2025》提出要提升輕量化材料等核心技術(shù)的工程化和產(chǎn)業(yè)化能力,同時(shí)推動(dòng)自主品牌節(jié)能與新能源汽車同國(guó)際先進(jìn)水平接軌。然而隨著鋼板強(qiáng)度的提升,傳統(tǒng)冷沖壓成形中往往存在開(kāi)裂、回彈、起皺等缺陷,同時(shí)成形力明顯增加又對(duì)壓力機(jī)和模具壽命提出更高的要求。為解決這些問(wèn)題,一種能夠降低成形力和成形難度,且成形后所得構(gòu)件兼具超高強(qiáng)度和高精度的先進(jìn)材料加工技術(shù)——熱沖壓技術(shù)應(yīng)運(yùn)而生。時(shí)至今日,熱沖壓成形技術(shù)已廣泛用于汽車車身及底盤結(jié)構(gòu)件成形制造中(圖1)。
熱沖壓成形技術(shù)的概念與特點(diǎn)
熱沖壓成形(Hot stamping)是國(guó)際上近幾年來(lái)出現(xiàn)的一項(xiàng)專門用于成形超高強(qiáng)度鋼板沖壓件的先進(jìn)制造技術(shù),也是汽車沖壓件制造領(lǐng)域內(nèi)的較為先進(jìn)的技術(shù)。熱沖壓成形技術(shù)包括直接熱沖壓和間接熱沖壓兩種形式。以最常用的直接熱沖壓成形為例,其工藝流程如圖2所示,首先將高強(qiáng)度硼鋼板坯料加熱到奧氏體化溫度以上,并保溫一定時(shí)間使其充分奧氏體化(通常為900~950℃),隨后將加熱的坯料迅速轉(zhuǎn)移至帶有冷卻系統(tǒng)的模具內(nèi)沖壓成形,同時(shí)保壓淬火,使構(gòu)件材料發(fā)生馬氏體轉(zhuǎn)變。與傳統(tǒng)的冷沖壓相比,鋼板在高溫時(shí)成形性好,可一次成形復(fù)雜形狀的構(gòu)件,并且構(gòu)件強(qiáng)度可達(dá)1500MPa甚至更高。此外,熱沖壓工藝的構(gòu)件回彈小、精度高、變形抗力約為冷沖壓的三分之一、設(shè)備噸位小。
圖1熱沖壓構(gòu)件在汽車上的應(yīng)用
圖2熱沖壓工藝流程
目前熱沖壓成形材料主要用22MnB5,包括鋁硅(Al-10Si)鍍層、GI/GA鍍層、鋅鎳(Zn-10Ni)鍍層、復(fù)合鍍層及其他涂層和裸板。作為典型的第三代先進(jìn)高強(qiáng)度鋼,將中錳鋼加熱至750℃即可獲得全奧氏體組織,擴(kuò)大了熱成形工藝窗口。
熱沖壓成形技術(shù)與裝備研究進(jìn)展
熱沖壓成形中所使用的鋼板是一種特殊的硼合金鋼板,這種鋼板不同于傳統(tǒng)的冷成形超高強(qiáng)鋼?,F(xiàn)在應(yīng)用比較廣泛的雙相鋼、復(fù)相鋼等冷成形高強(qiáng)度鋼板一般是在常溫下通過(guò)冷沖壓的方法成形,成形前后零件的顯微組織和機(jī)械強(qiáng)度基本不發(fā)生改變。而熱沖壓成形中所使用的鋼板在常溫下強(qiáng)度不很高,抗拉強(qiáng)度僅有400~600MPa,具有良好的塑性與可成形性;它是通過(guò)熱沖壓成形工藝進(jìn)行成形和淬火后,零件的顯微組織由原來(lái)的鐵素體和珠光體轉(zhuǎn)變成均勻的馬氏體,抗拉強(qiáng)度可以達(dá)到1500MPa以上,硬度可以達(dá)到50HRC,而且基本沒(méi)有回彈,具有很高的尺寸精度。在鋼板中添加了硼,其目的在于提高鋼板的淬火性能,使板料的組織轉(zhuǎn)變順利進(jìn)行。此外,為了提高材料的強(qiáng)度以及其它力學(xué)性能,還添加了Ti、Cr、Mo、Cu、Ni等多種合金微量元素。本研究團(tuán)隊(duì)在中國(guó)汽車產(chǎn)業(yè)創(chuàng)新發(fā)展聯(lián)合基金(編號(hào):U1564202)、湖北省技術(shù)創(chuàng)新專項(xiàng)重大項(xiàng)目(編號(hào):2016AAA053)等資助下,圍繞超高強(qiáng)度硼鋼熱沖壓成形機(jī)理、技術(shù)及裝備開(kāi)展了相關(guān)研究。
高強(qiáng)鋼熱沖壓成形過(guò)程中不僅包含塑性變形過(guò)程,還包含溫度變化及組織演變過(guò)程,是一個(gè)典型的熱-力-相變耦合的過(guò)程。為準(zhǔn)確實(shí)現(xiàn)熱沖壓變形規(guī)律預(yù)測(cè)和缺陷控制,建立了耦合位錯(cuò)密度和損傷演化的材料本構(gòu)模型和成形極限模型。圖3所示為耦合位錯(cuò)密度的熱沖壓硼鋼高溫本構(gòu)模型。
熱沖壓汽車構(gòu)件組織性能協(xié)同控制技術(shù)
研究團(tuán)隊(duì)提出了基于急動(dòng)度的伺服熱沖壓工藝設(shè)計(jì)方法,能夠有效地控制沖壓速度和成形溫度,提升成形效果;研發(fā)了低溫?zé)釠_壓專利技術(shù),降低連續(xù)生產(chǎn)時(shí)的模具溫度、縮短保溫時(shí)間、節(jié)約成本;研發(fā)了熱沖壓汽車構(gòu)件組織性能協(xié)同控制技術(shù),以改善高強(qiáng)度鋼板熱沖壓件綜合性能和精度;建立了A柱、B柱、C柱、前縱梁、保險(xiǎn)杠等汽車安全結(jié)構(gòu)件熱沖壓全過(guò)程有限元模型,可以有效預(yù)測(cè)零件成形性、減薄率、馬氏體含量及抗拉強(qiáng)度的變化(圖4)。
圖3耦合位錯(cuò)密度的熱沖壓硼鋼高溫本構(gòu)模型
圖4幾種不同汽車構(gòu)件的熱沖壓模擬結(jié)果
通過(guò)伺服熱沖壓及組織性能協(xié)同調(diào)控技術(shù),對(duì)B柱等樣件進(jìn)行了試制(圖5)。對(duì)不同部位進(jìn)行力學(xué)性能檢測(cè),結(jié)果表明不同區(qū)域的試樣抗拉強(qiáng)度基本在1500~1600MPa,延伸率范圍為8%~13%(目前文獻(xiàn)資料中多數(shù)報(bào)道為5%~8%),其微觀組織的主要成分為馬氏體,夾雜有少量殘余奧氏體。此外還對(duì)零件的成形精度進(jìn)行了檢測(cè)分析,產(chǎn)品關(guān)鍵點(diǎn)尺寸誤差不超過(guò)±0.21mm(圖6)。試驗(yàn)結(jié)果表明,相關(guān)樣件已實(shí)現(xiàn)了組織強(qiáng)韌性和精度的協(xié)同控制,完全滿足裝車要求。目前此項(xiàng)技術(shù)已實(shí)現(xiàn)了技術(shù)轉(zhuǎn)化和產(chǎn)業(yè)化。
圖5 B柱熱沖壓樣件及關(guān)鍵區(qū)域的馬氏體組織形貌
圖6 B柱熱沖壓樣件精度檢測(cè)結(jié)果
梯度力學(xué)性能熱沖壓構(gòu)件設(shè)計(jì)制造一體化技術(shù)
傳統(tǒng)的熱沖壓成形工藝,板料的各個(gè)位置變形條件基本相同,所以得到的熱沖壓零件基本為全馬氏體組織,抗拉強(qiáng)度達(dá)1500MPa甚至更高。但是延伸率相對(duì)較低,造成零件塑性或韌性急劇降低、冷彎性能差。一旦發(fā)生碰撞,熱沖壓結(jié)構(gòu)件的碰撞吸能效果大大降低。
為進(jìn)一步提升熱沖壓構(gòu)件的碰撞吸能性能,采用側(cè)碰吸能分析方法對(duì)其進(jìn)行了梯度力學(xué)性能優(yōu)化設(shè)計(jì)(圖7),得到了具有合理梯度力學(xué)性能分布的B柱構(gòu)件,相關(guān)梯度力學(xué)性能設(shè)計(jì)方案如圖8所示。結(jié)果表明,應(yīng)用梯度力學(xué)性能,B柱可以簡(jiǎn)化B柱總成結(jié)構(gòu),達(dá)到減重12.1%的輕量化目的,且能夠很好地兼顧強(qiáng)度與碰撞吸能性能。陶瓷熱障涂層專利技術(shù)制造的梯度力學(xué)性能樣件如圖9所示。
圖7整車側(cè)面碰撞有限元模型
圖8 B柱梯度力學(xué)性能區(qū)域位置設(shè)計(jì)方案
圖9梯度力學(xué)性能熱沖壓B柱樣件
具有隨形冷卻水道的超高強(qiáng)度鋼熱沖壓模具
與冷沖壓模具不同,熱沖壓模具除了具有成形功能外,還具有冷卻淬火功能。為了保證其冷卻效果,在其內(nèi)部設(shè)有冷卻管道,模具結(jié)構(gòu)更加復(fù)雜,對(duì)模具材料的選擇及結(jié)構(gòu)設(shè)計(jì)等方面要求更為嚴(yán)格。
熱沖壓成形模具冷卻系統(tǒng)的設(shè)計(jì)需要考慮加工方式、冷卻均勻性等方面,因此冷卻管直徑、冷卻管間距、冷卻管距模具型面距離等參數(shù)都是設(shè)計(jì)的關(guān)鍵,筆者所在的研究團(tuán)隊(duì)對(duì)熱沖壓B柱加強(qiáng)板采用鑲塊式模具結(jié)構(gòu)。為實(shí)現(xiàn)構(gòu)件冷卻效果并保證模具的強(qiáng)度,采用與模具型面相近的隨形冷卻水道。模芯鑲塊內(nèi)部與鑲塊之間冷卻水管道采用直徑φ10mm的孔,相鄰冷卻水管道中心距約為17~20mm,冷卻水管道中心距最近型面距離為15~20mm。每個(gè)鑲塊都配給相對(duì)獨(dú)立的進(jìn)出水冷卻系統(tǒng),相鄰鑲塊之間冷卻水道不連通。采用ANSYS CFX進(jìn)行流固耦合數(shù)值模擬,并對(duì)凸凹模的冷卻水流速及溫度均勻性進(jìn)行分析。第六個(gè)工藝循環(huán)模具冷卻水熱傳遞系數(shù)云圖如圖10所示,圖中冷卻水流速快的中央部位HTC值最高,大部分位置HTC均大于10000W/(m2·K),說(shuō)明冷卻效果較好,可以滿足連續(xù)生產(chǎn)所需的冷卻效果。圖11為加工制造完成后的模具實(shí)物圖
熱沖壓成形由以下幾個(gè)工序組成:
1.落料:
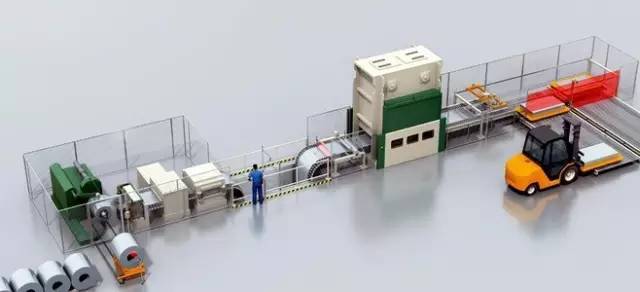
是熱沖壓成形中的第一道工序,把板材沖壓出所需外輪廓坯料。
2.奧氏體化:
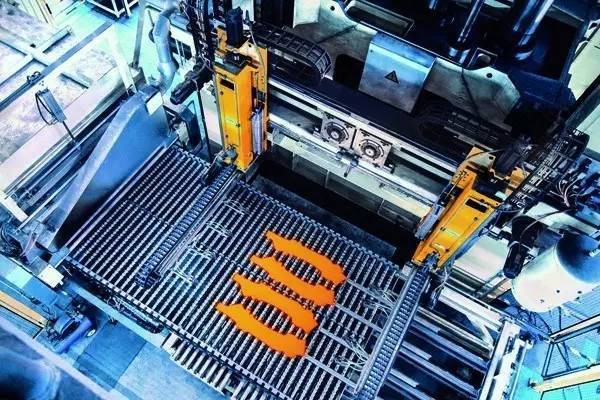
包括加熱和保溫兩個(gè)階段。這一工序的目的在于將鋼板加熱到一個(gè)合適的溫度,使鋼板完全奧氏體化,并且具有良好的塑性。加熱所使用的設(shè)備為專用的連續(xù)加熱爐,鋼板在加熱到再結(jié)晶溫度以上之后,表面很容易氧化,生成氧化皮,這層氧化皮會(huì)對(duì)后續(xù)的加工造成不利的影響。為了避免或減少鋼板在加熱爐中的氧化,一般在加熱爐內(nèi)設(shè)置惰性氣體保護(hù)機(jī)制,或者對(duì)板料進(jìn)行表面防氧化處理。
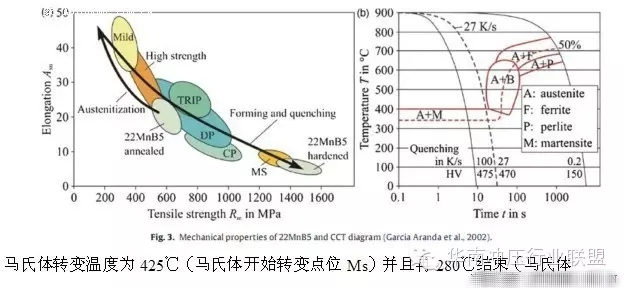
3.轉(zhuǎn)移:
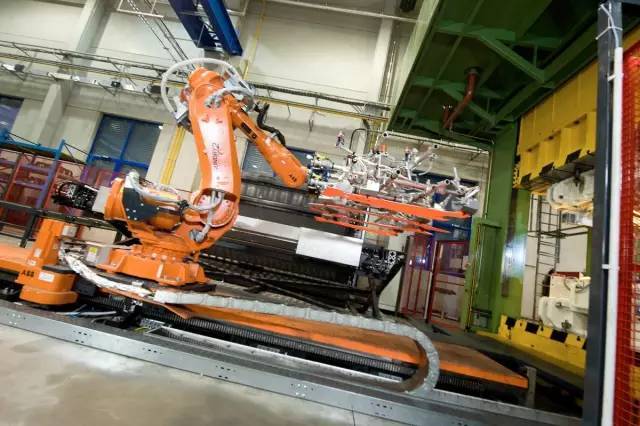
指的是將加熱后的鋼板從加熱爐中取出放進(jìn)熱成形模具中去。在這一道工序中,必須保證鋼板被盡可能快地轉(zhuǎn)移到模具中,一方面是為了防止高溫下的鋼板氧化,另一方面是為了確保鋼板在成形時(shí)仍然處在較高的溫度下,以具有良好的塑性。
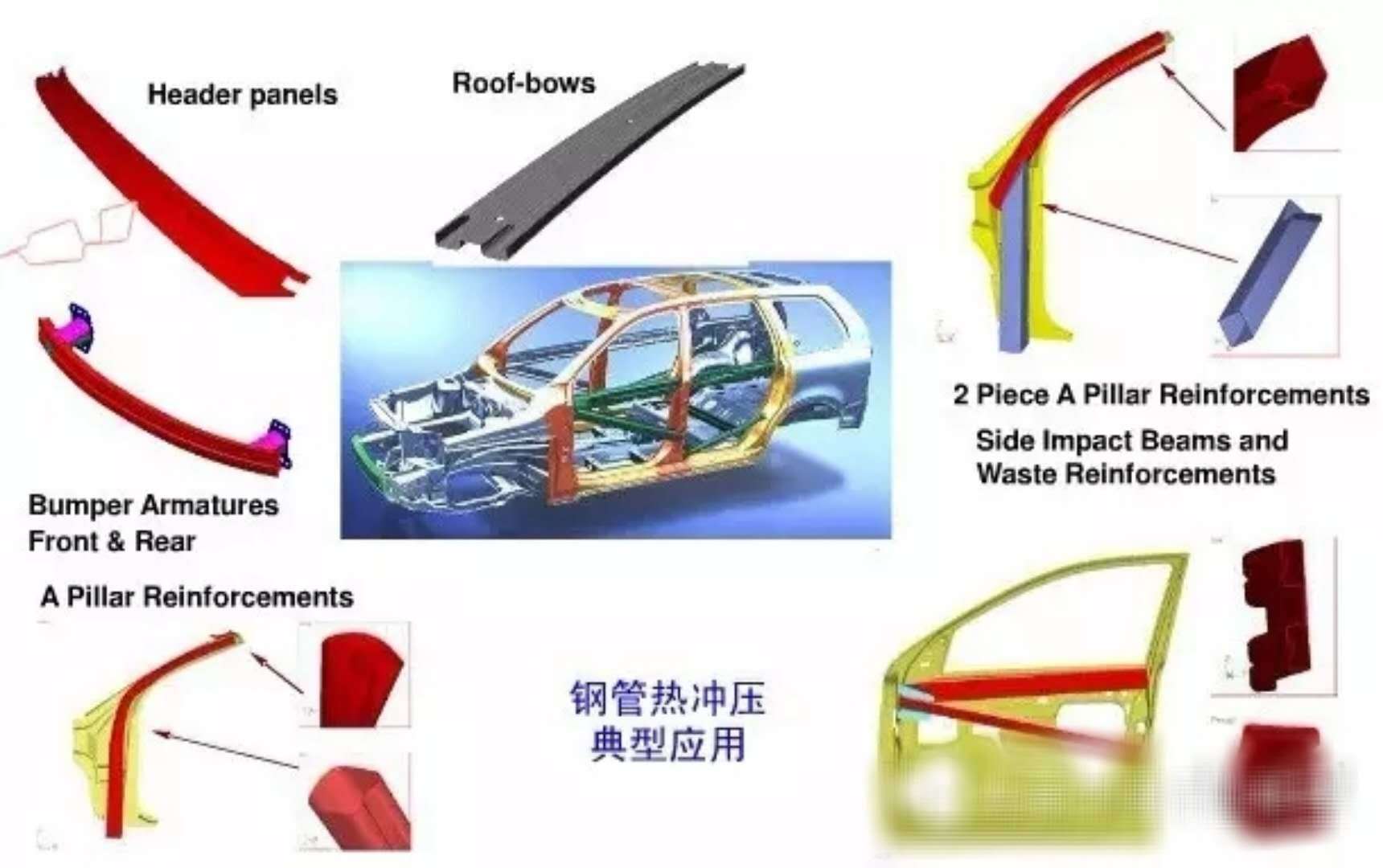
4.沖壓和淬火:
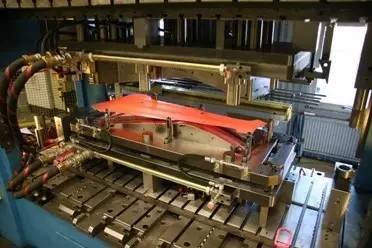
在將鋼板放進(jìn)模具之后,要立即對(duì)鋼板進(jìn)行沖壓成形,以免溫度下降過(guò)多影響鋼板的成形性能。成形以后模具要合模保壓一段時(shí)間,一方面是為了控制零件的形狀,另一方面是利用模具中設(shè)置的冷卻裝置對(duì)鋼板進(jìn)行淬火,使零件形成均勻的馬氏體組織,獲得良好的尺寸精度和機(jī)械性能。研究表明,就目前常用的熱沖壓鋼材而言,實(shí)現(xiàn)奧氏體向馬氏體轉(zhuǎn)變的最小冷卻速率為27~30℃/s,因此要保證模具對(duì)板料的冷卻速度大于此臨界值。
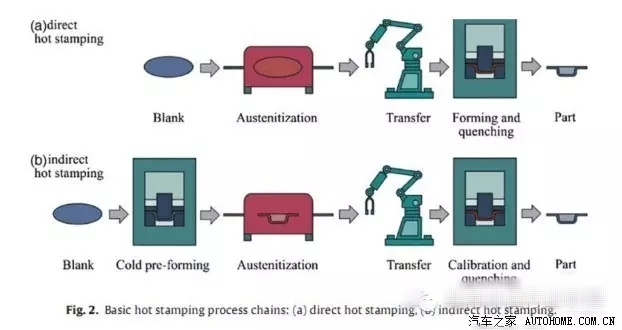
5.后續(xù)處理:
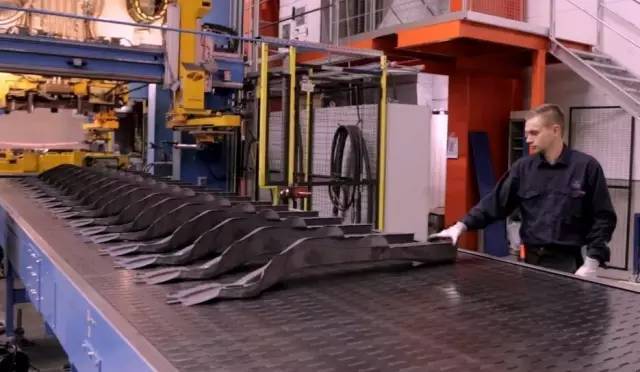
在成形件從模具中取出以后,還需要對(duì)其進(jìn)行一些后續(xù)的處理,如利用酸洗或噴丸的方式去除零件表面的氧化皮,以及對(duì)零件進(jìn)行切邊和鉆孔。熱沖壓件由于強(qiáng)度太高,不能用傳統(tǒng)的手段對(duì)其進(jìn)行切邊及鉆孔加工,而必須用激光技術(shù)來(lái)完成。
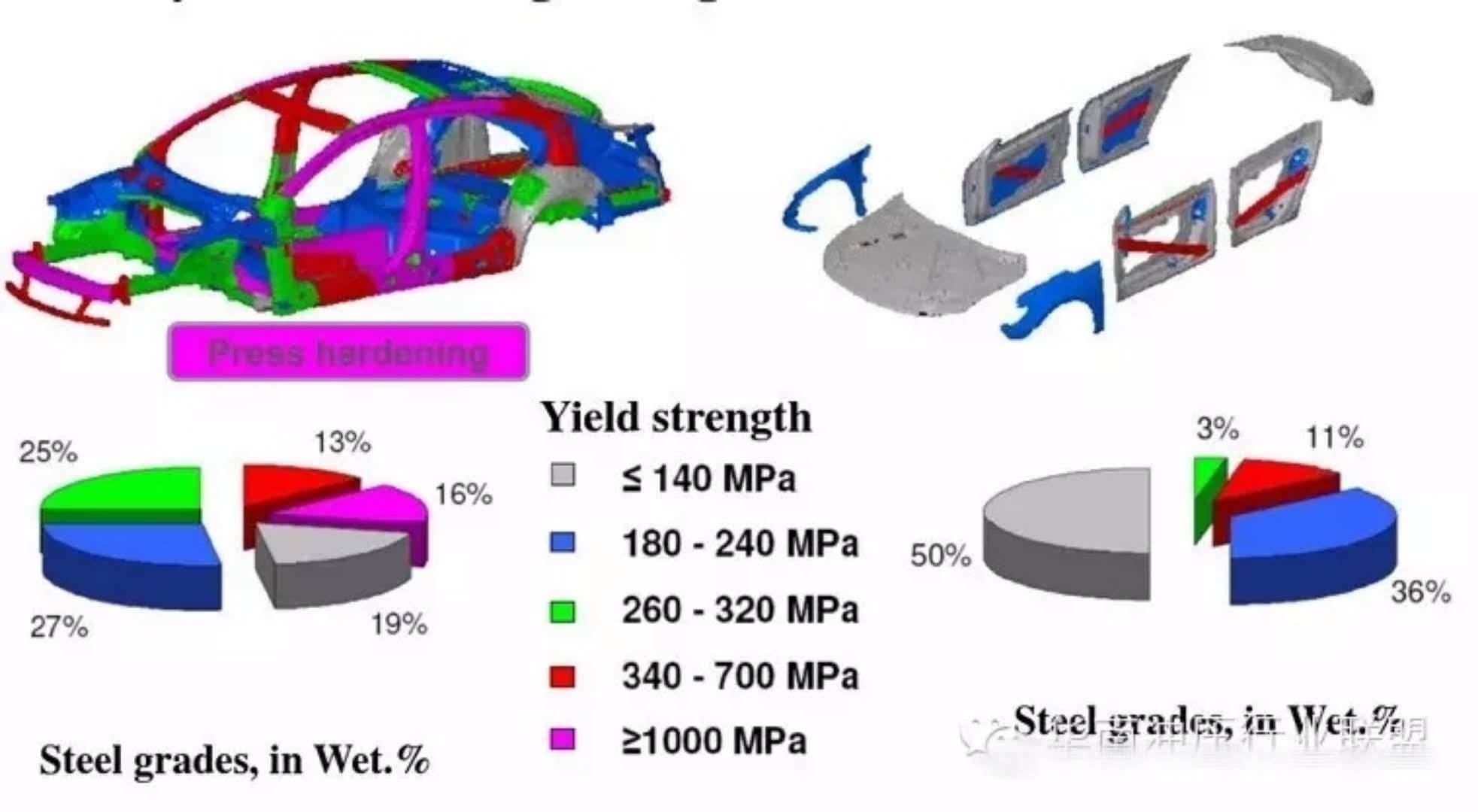
熱沖壓模具設(shè)計(jì)是熱沖壓成形工藝的核心技術(shù),它不僅要滿足零件的成形需要,而且還要具有優(yōu)異的冷卻能力,以保證零件獲得良好的機(jī)械性能和尺寸精度。
熱沖壓成型的優(yōu)缺點(diǎn):
先進(jìn)熱沖壓生產(chǎn)示范線的建立
先進(jìn)的輕量化車身結(jié)構(gòu)件伺服熱沖壓成形示范線,主要裝備包含高速伺服壓力機(jī)、數(shù)控加熱爐、熱沖壓模具、低自由度桁架機(jī)器人、激光切割機(jī)和噴丸裝備等主要裝備(圖12)。通過(guò)運(yùn)用工業(yè)以太網(wǎng)技術(shù)實(shí)現(xiàn)裝備平臺(tái)的互聯(lián)互鎖,可以完成滿足工業(yè)生產(chǎn)節(jié)拍需求的加熱、成形-保壓淬火和上、下料全過(guò)程各項(xiàng)功能及安全防護(hù)要求,形成了具有自主知識(shí)產(chǎn)權(quán)的伺服熱沖壓成形生產(chǎn)線的設(shè)計(jì)方法。
圖10第六個(gè)工藝循環(huán)模具冷卻水熱傳遞系數(shù)云圖
圖11 B柱加強(qiáng)板熱沖壓模具實(shí)物圖
圖12熱沖壓生產(chǎn)示范線
結(jié)束語(yǔ)
作為汽車輕量化的重要途徑,超高強(qiáng)度鋼板熱沖壓成形技術(shù)正在被世界各國(guó)企業(yè)和學(xué)者廣泛關(guān)注。系統(tǒng)地、深層次地開(kāi)展相關(guān)研究,形成具有完全自主知識(shí)產(chǎn)權(quán)的熱沖壓成形工藝及裝備關(guān)鍵技術(shù),對(duì)我國(guó)汽車行業(yè)的發(fā)展具有十分重要的現(xiàn)實(shí)意義。
——來(lái)源:《鍛造與沖壓》2018年第22期
以上就是100唯爾(100vr.com)小編為您介紹的關(guān)于鍛造與沖壓的知識(shí)技巧了,學(xué)習(xí)以上的鍛造與沖壓:汽車輕量化之路,原來(lái)還能在這個(gè)方面發(fā)力!汽車熱沖壓成形(Hot Stamping)的技術(shù)要點(diǎn)解析!知識(shí),對(duì)于鍛造與沖壓的幫助都是非常大的,這也是新手學(xué)習(xí)機(jī)械制造所需要注意的地方。如果使用100唯爾還有什么問(wèn)題可以點(diǎn)擊右側(cè)人工服務(wù),我們會(huì)有專業(yè)的人士來(lái)為您解答。
本站在轉(zhuǎn)載文章時(shí)均注明來(lái)源出處,轉(zhuǎn)載目的在于傳遞更多信息,未用于商業(yè)用途。如因本站的文章、圖片等在內(nèi)容、版權(quán)或其它方面存在問(wèn)題或異議,請(qǐng)與本站聯(lián)系(電話:0592-5551325,郵箱:help@onesoft.com.cn),本站將作妥善處理。
鍛造與沖壓課程推薦
機(jī)械制造熱門資料
機(jī)械制造技術(shù)文檔
- 1?呼和浩特工務(wù)段卓資東高鐵實(shí)訓(xùn)場(chǎng)建設(shè)項(xiàng)目議價(jià)采購(gòu)二次公告
- 2鐵小微帶你看:大南鐵國(guó)家高鐵實(shí)訓(xùn)基地,超牛!
- 3尚義職教中心首屆高鐵專業(yè)學(xué)生赴北京實(shí)習(xí)實(shí)訓(xùn)
- 4技能展示 | 高鐵專業(yè)實(shí)訓(xùn)技能展示
- 5磨礪青春、出彩中職——高鐵專業(yè)實(shí)訓(xùn)風(fēng)采
- 6陜西長(zhǎng)城鐵路技師學(xué)院,一所把高鐵實(shí)訓(xùn)搬進(jìn)課堂的高等院校
- 7喜訊!喜訊!1:1仿真高鐵實(shí)訓(xùn)設(shè)備進(jìn)入梧州電子科技學(xué)校
- 8云南工程職業(yè)學(xué)院高鐵實(shí)訓(xùn)基地建成啟用
- 9高鐵實(shí)訓(xùn)課走進(jìn)無(wú)錫東站!
- 10職教標(biāo)準(zhǔn)I高等職業(yè)學(xué)校城市軌道交通通信信號(hào)技術(shù)教學(xué)標(biāo)準(zhǔn)
推薦閱讀
